In the realm of precision manufacturing, where even the slightest imperfection can compromise the integrity and performance of a product, the choice of surface treatment techniques becomes paramount. This article delves into the comparison between laser cleaning machines and traditional grinding methods, with a focus on the Trolley Laser Cleaning Machine, highlighting its unique features and applicability in precision manufacturing scenarios.
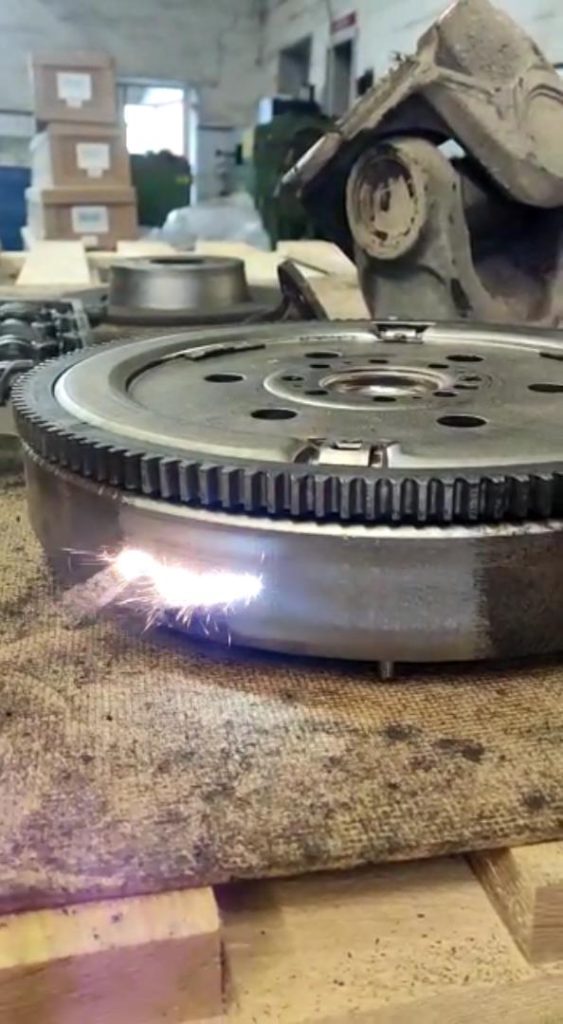
Introduction
Precision manufacturing demands meticulous attention to detail, ensuring that every component is flawlessly prepared for assembly or end-use. When it comes to surface cleaning and preparation, two primary techniques stand out: laser cleaning and traditional grinding. While both have their merits, the Trolley Laser Cleaning Machine, with its innovative design and eco-friendly operation, offers a compelling alternative to traditional methods.
Laser Cleaning Machine: A Modern Solution
The Trolley Laser Cleaning Machine represents the cutting edge of surface treatment technology, integrating advanced laser technology with user-friendly design. Its key features and advantages are as follows:
Ultra-High Frequency Air-Cooled Pulsed Fiber Laser
– Efficiency & Precision: The ultra-high frequency air-cooled pulsed fiber laser ensures rapid and precise cleaning, minimizing heat input and protecting the substrate from thermal damage.
– No Warm-Up Time: Air-cooled design eliminates the need for warm-up, allowing for immediate use and increased productivity.
Simple Operation & Efficient Multiple Laser Cleaning Patterns
– Ease of Use: The machine boasts a straightforward operation interface, enabling operators to quickly and easily switch between cleaning patterns tailored to specific tasks.
– Versatility: Multiple cleaning patterns cater to diverse surface conditions, ensuring optimal results across various applications.
Luggage-style Fully Enclosed Design & Mini Cleaning Head
– Portability & Safety: The luggage-style fully enclosed design combined with a mini cleaning head makes the machine lightweight and convenient for transportation and use in confined spaces.
– Protection: The enclosed design also offers protection to the laser source and optical components, ensuring long-term reliability.
Eco-Friendly & Energy-Efficient
– Green Cleaning: The laser cleaning process eliminates the need for chemicals and other media, making it an environmentally friendly alternative to traditional methods.
– Energy Savings: With support for single-phase 110V and 307V power supplies, the machine operates efficiently, reducing energy consumption.
Application Scenarios in Precision Manufacturing
The Trolley Laser Cleaning Machine is ideally suited for precision manufacturing applications where surface quality is critical. Some key scenarios include:
– Metal Surface Texturing Treatment: Precisely controlled laser cleaning can enhance surface textures, preparing metal components for subsequent processes such as coating or plating.
– Maintenance of Stone Artworks, Cultural Relics, Sculptures: Non-destructive and non-contact cleaning ensures delicate stone artworks, cultural relics, and sculptures remain undamaged during cleaning.
– Oxide, Rust, & Paint Removal: Effective removal of surface oxides, rust, and paint layers without damaging the underlying material, crucial for restoring metal parts to their original condition.
– Oil Stain Removal in Food Industry: Quickly and safely remove oil stains from utensils and equipment in the food industry, without the use of harmful organic solvents.
Conclusion
In the context of precision manufacturing, the Trolley Laser Cleaning Machine emerges as a superior choice over traditional grinding methods. Its precision, eco-friendliness, and versatility make it an invaluable tool for achieving flawless surface preparation. As the demand for higher-quality, precision-engineered products continues to grow, laser cleaning machines will undoubtedly play an increasingly important role in the manufacturing landscape.